Budowa maszyn pneumatycznych opiera się na kilku kluczowych elementach, które decydują o ich funkcjonalności i efektywności. Podstawowym komponentem jest sprężarka, która odpowiada za wytwarzanie sprężonego powietrza. Sprężarki mogą być różnego rodzaju, w tym tłokowe, śrubowe czy wirnikowe, a ich wybór zależy od specyfiki zastosowania. Kolejnym istotnym elementem są zbiorniki na sprężone powietrze, które magazynują energię i zapewniają jej stabilne dostarczanie do układów roboczych. W systemach pneumatycznych niezbędne są także zawory sterujące, które regulują przepływ powietrza oraz jego ciśnienie. Zawory te mogą być ręczne lub automatyczne, co wpływa na wygodę użytkowania i precyzję działania maszyny. Rury i przewody pneumatyczne stanowią kolejny ważny element, ponieważ transportują sprężone powietrze do różnych części maszyny. Dobrze zaprojektowany układ rur minimalizuje straty ciśnienia i zapewnia efektywność całego systemu.
Jakie są zalety maszyn pneumatycznych w przemyśle
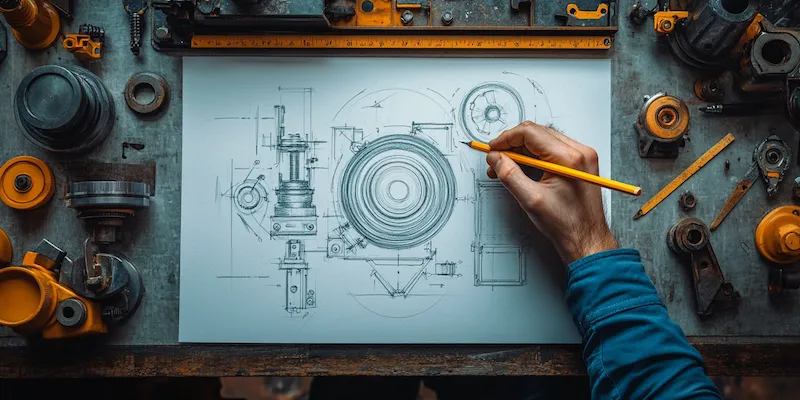
Maszyny pneumatyczne cieszą się dużą popularnością w przemyśle ze względu na swoje liczne zalety. Przede wszystkim charakteryzują się one dużą wydajnością i szybkością działania, co jest kluczowe w wielu procesach produkcyjnych. Dzięki zastosowaniu sprężonego powietrza jako medium roboczego, maszyny te są również bezpieczne w użyciu, ponieważ nie stwarzają ryzyka wybuchu ani pożaru, jak ma to miejsce w przypadku maszyn elektrycznych czy hydraulicznych. Kolejną istotną zaletą jest ich prostota konstrukcji oraz łatwość w utrzymaniu. W porównaniu do innych systemów napędowych, maszyny pneumatyczne wymagają mniej skomplikowanej obsługi technicznej, co przekłada się na niższe koszty eksploatacji. Dodatkowo, maszyny te są elastyczne i można je łatwo dostosować do zmieniających się potrzeb produkcyjnych. Wiele z nich można szybko modyfikować lub rozbudowywać, co pozwala na optymalizację procesów bez konieczności inwestowania w nowe urządzenia.
Jakie są zastosowania maszyn pneumatycznych w różnych branżach
Maszyny pneumatyczne znajdują szerokie zastosowanie w różnych branżach przemysłu ze względu na swoją wszechstronność i efektywność. W przemyśle motoryzacyjnym są wykorzystywane do montażu elementów oraz do malowania pojazdów, gdzie precyzyjne dozowanie farby jest kluczowe dla jakości wykończenia. W branży spożywczej maszyny pneumatyczne służą do pakowania produktów oraz transportu surowców, takich jak zboża czy płyny. Dzięki możliwości sterowania procesami za pomocą sprężonego powietrza można osiągnąć wysoką wydajność oraz bezpieczeństwo higieniczne. W budownictwie natomiast maszyny te są wykorzystywane do podnoszenia ciężkich materiałów oraz do wykonywania prac wykończeniowych. W sektorze medycznym maszyny pneumatyczne znajdują zastosowanie przy produkcji sprzętu medycznego oraz w laboratoriach analitycznych, gdzie precyzyjne pomiary i kontrola ciśnienia są niezwykle istotne. Również w branży elektronicznej wykorzystuje się je do montażu podzespołów oraz testowania urządzeń elektronicznych.
Jakie są nowoczesne technologie w budowie maszyn pneumatycznych
Nowoczesne technologie znacząco wpłynęły na rozwój budowy maszyn pneumatycznych, wprowadzając innowacyjne rozwiązania zwiększające ich efektywność i funkcjonalność. Jednym z takich rozwiązań jest automatyzacja procesów za pomocą systemów sterowania PLC (Programmable Logic Controller), które umożliwiają precyzyjne zarządzanie pracą maszyn oraz monitorowanie ich stanu w czasie rzeczywistym. Dzięki temu możliwe jest szybkie reagowanie na ewentualne awarie oraz optymalizacja cykli produkcyjnych. Kolejnym nowoczesnym rozwiązaniem jest zastosowanie technologii IoT (Internet of Things), która pozwala na zdalne monitorowanie i zarządzanie maszynami pneumatycznymi poprzez internet. Umożliwia to zbieranie danych dotyczących wydajności oraz stanu technicznego urządzeń, co przyczynia się do lepszego planowania konserwacji i minimalizacji przestojów produkcyjnych. Warto również zwrócić uwagę na rozwój materiałów stosowanych w budowie komponentów pneumatycznych, takich jak lekkie stopy metali czy tworzywa sztuczne o wysokiej wytrzymałości, co wpływa na obniżenie masy urządzeń oraz zwiększenie ich trwałości.
Jakie są wyzwania w budowie maszyn pneumatycznych
Budowa maszyn pneumatycznych, mimo licznych zalet, wiąże się również z pewnymi wyzwaniami, które inżynierowie i projektanci muszą brać pod uwagę. Jednym z głównych problemów jest konieczność zapewnienia odpowiedniego ciśnienia sprężonego powietrza w systemie. Niewłaściwe ciśnienie może prowadzić do obniżenia wydajności maszyny oraz zwiększenia ryzyka awarii. Dlatego tak istotne jest dokładne zaplanowanie układu pneumatycznego oraz regularne monitorowanie jego stanu. Kolejnym wyzwaniem jest dobór odpowiednich materiałów, które będą odporne na działanie sprężonego powietrza oraz na różnorodne warunki pracy. W przypadku niektórych aplikacji, takich jak przemysł chemiczny czy spożywczy, materiały muszą spełniać dodatkowe normy dotyczące bezpieczeństwa i higieny. Problematyczne mogą być również straty energii związane z nieszczelnościami w układzie pneumatycznym. Nawet niewielkie wycieki mogą prowadzić do znacznych strat finansowych oraz obniżenia efektywności całego systemu. Dlatego projektanci muszą zwracać szczególną uwagę na jakość wykonania połączeń oraz stosować odpowiednie uszczelnienia.
Jakie są przyszłe kierunki rozwoju maszyn pneumatycznych
Przyszłość maszyn pneumatycznych zapowiada się obiecująco, a ich rozwój będzie związany z kilkoma kluczowymi kierunkami. Przede wszystkim można spodziewać się dalszej automatyzacji procesów produkcyjnych, co pozwoli na zwiększenie wydajności i precyzji działania maszyn. Wprowadzenie sztucznej inteligencji do systemów sterowania umożliwi lepsze prognozowanie awarii oraz optymalizację cykli produkcyjnych na podstawie analizy danych historycznych. Również rozwój technologii IoT będzie miał znaczący wpływ na przyszłość maszyn pneumatycznych, umożliwiając zdalne monitorowanie i zarządzanie urządzeniami w czasie rzeczywistym. Dzięki temu przedsiębiorstwa będą mogły szybciej reagować na ewentualne problemy oraz lepiej planować konserwację. Kolejnym kierunkiem rozwoju będzie poszukiwanie bardziej ekologicznych rozwiązań, które ograniczą zużycie energii oraz emisję hałasu podczas pracy maszyn pneumatycznych. Innowacyjne technologie odzyskiwania energii oraz zastosowanie materiałów biodegradowalnych w budowie komponentów mogą przyczynić się do zmniejszenia negatywnego wpływu na środowisko.
Jakie są koszty związane z budową maszyn pneumatycznych
Koszty związane z budową maszyn pneumatycznych mogą być bardzo zróżnicowane i zależą od wielu czynników, takich jak rodzaj maszyny, jej skomplikowanie oraz zastosowane technologie. Na początku warto zwrócić uwagę na koszty zakupu komponentów, takich jak sprężarki, zbiorniki czy siłowniki pneumatyczne. Ceny tych elementów mogą się znacznie różnić w zależności od producenta oraz jakości materiałów użytych do ich produkcji. Dodatkowo należy uwzględnić koszty montażu i uruchomienia maszyny, które mogą być znaczące w przypadku bardziej skomplikowanych systemów. Koszt eksploatacji maszyn pneumatycznych również powinien być brany pod uwagę, ponieważ obejmuje on wydatki na energię elektryczną potrzebną do pracy sprężarek oraz regularne przeglądy techniczne i konserwację urządzeń. Warto także pamiętać o kosztach związanych z ewentualnymi naprawami w przypadku awarii, które mogą być nieprzewidywalne i znacząco wpłynąć na budżet przedsiębiorstwa.
Jakie są najczęstsze błędy przy budowie maszyn pneumatycznych
Podczas budowy maszyn pneumatycznych często popełniane są błędy, które mogą prowadzić do obniżenia efektywności ich działania lub nawet do awarii. Jednym z najczęstszych błędów jest niewłaściwe dobranie komponentów do konkretnego zastosowania. Na przykład wybór sprężarki o niewłaściwej mocy może skutkować niedoborem lub nadmiarem sprężonego powietrza w systemie, co negatywnie wpłynie na jego wydajność. Innym powszechnym problemem jest niewłaściwe zaprojektowanie układu rur i przewodów pneumatycznych, co może prowadzić do strat ciśnienia oraz zwiększonego zużycia energii. Nieszczelności w połączeniach to kolejny istotny błąd, który może generować znaczne straty finansowe związane z utratą sprężonego powietrza. Ponadto brak regularnej konserwacji i przeglądów technicznych może prowadzić do poważnych awarii oraz skrócenia żywotności maszyny.
Jakie są przykłady innowacyjnych rozwiązań w budowie maszyn pneumatycznych
Innowacyjne rozwiązania w budowie maszyn pneumatycznych pojawiają się coraz częściej dzięki postępowi technologicznemu oraz rosnącym wymaganiom rynku. Przykładem takiego rozwiązania są inteligentne siłowniki pneumatyczne wyposażone w czujniki monitorujące parametry pracy, takie jak ciśnienie czy prędkość ruchu. Dzięki tym danym możliwe jest optymalizowanie procesów produkcyjnych oraz szybsze wykrywanie ewentualnych usterek. Kolejnym innowacyjnym rozwiązaniem są systemy zarządzania energią sprężonego powietrza, które pozwalają na efektywne wykorzystanie dostępnej energii poprzez automatyczne dostosowywanie ciśnienia do aktualnych potrzeb produkcyjnych. Wprowadzenie technologii odzyskiwania energii również przyczynia się do zwiększenia efektywności energetycznej maszyn pneumatycznych poprzez wykorzystanie nadmiaru energii generowanej podczas pracy urządzeń do innych celów produkcyjnych.
Jakie są kluczowe aspekty bezpieczeństwa przy budowie maszyn pneumatycznych
Bezpieczeństwo przy budowie maszyn pneumatycznych jest niezwykle istotnym zagadnieniem, które powinno być brane pod uwagę już na etapie projektowania urządzeń. Kluczowym aspektem jest zapewnienie odpowiednich zabezpieczeń przed nadmiernym ciśnieniem wewnętrznym w układzie pneumaticznym, co może prowadzić do niebezpiecznych sytuacji lub uszkodzenia maszyny. W tym celu stosuje się zawory bezpieczeństwa oraz manometry monitorujące ciśnienie robocze systemu. Kolejnym ważnym elementem jest ergonomia stanowiska pracy operatora maszyny – odpowiednie rozmieszczenie elementów sterujących oraz zapewnienie łatwego dostępu do miejsc serwisowych wpływa na komfort pracy oraz minimalizuje ryzyko wystąpienia wypadków podczas obsługi urządzenia. Niezwykle istotne jest także regularne szkolenie pracowników dotyczące zasad BHP oraz obsługi maszyn pneumatycznych, aby byli świadomi potencjalnych zagrożeń i umieli reagować w sytuacjach kryzysowych.